Why the time is right for carton converters to capitalise on digital transformation
Key mega trends shaping carton manufacturing and how the latest technology responds shared at customer event
The trends and drivers shaping the future of carton manufacturing were identified and discussed last month when Koenig & Bauer Durst invited carton printers to Radebeul, Germany, home of the sheetfed production centre.
Around 100 interested carton converters, from across Europe and North America, listened to the wide-ranging discussions and learned more about Koenig & Bauer Durst’s solution to help them capitalise on emerging opportunities.
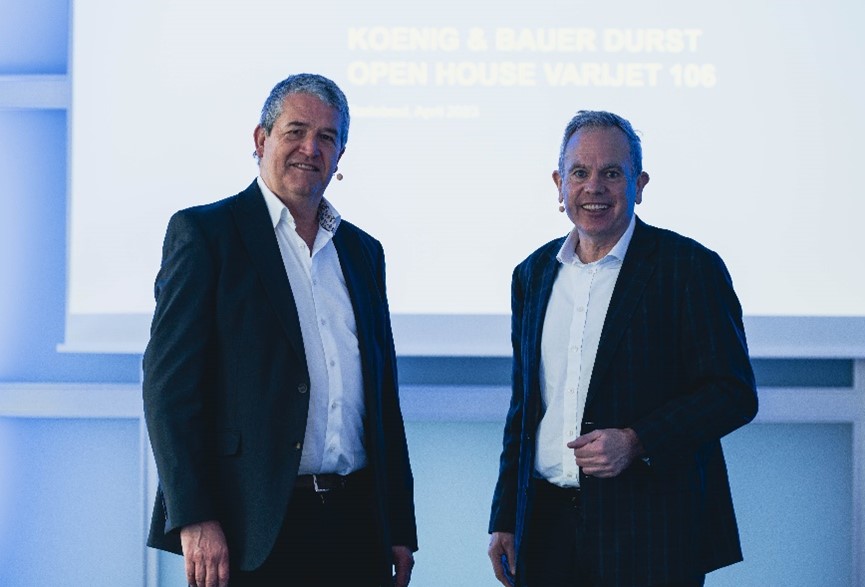
VariJET 106 Open House keynote Speaker Dr Sean Smyth (left) with Robert Stabler at the event
After Ralf Sammeck, Member of the Board at Koenig & Bauer with responsibility for Sheetfed, joined Koenig & Bauer Managing Director Robert Stabler to officially open the event, Dr Sean Smyth, print technologist and consultant for Smithers, listed the mega trends influencing today’s packaging environment.
They included sustainability and carton production’s place in a circular economy. Also detailed were the advantages of digital printing in eliminating the need for plates, water, and chemistry, and reducing set up time and waste, while improving responsiveness to demand.
The impact of micro and macroeconomics were explored – demographic shifts from the growth in affluent, educated consumers, to changing population age profiles and the rise in individual preferences. Sean expanded on how technology specific to packaging is evolving to deliver higher quality in an increasingly agile and responsive way.
Legislation is also shaping printing requirements both in terms of on pack information and post use disposal while enhanced supply chain management and track and trace capabilities enable improved stock oversight and brand protection.
These, he said, were set against a back drop of positive growth for carton makers in 2022. Growth that is expected to continue with cartons predicted to reach the equivalent of a billion A4 prints by 2028 and digital carton volumes in North America and Europe predicted to enjoy a compound annual growth rate of just under 20% to 2027.
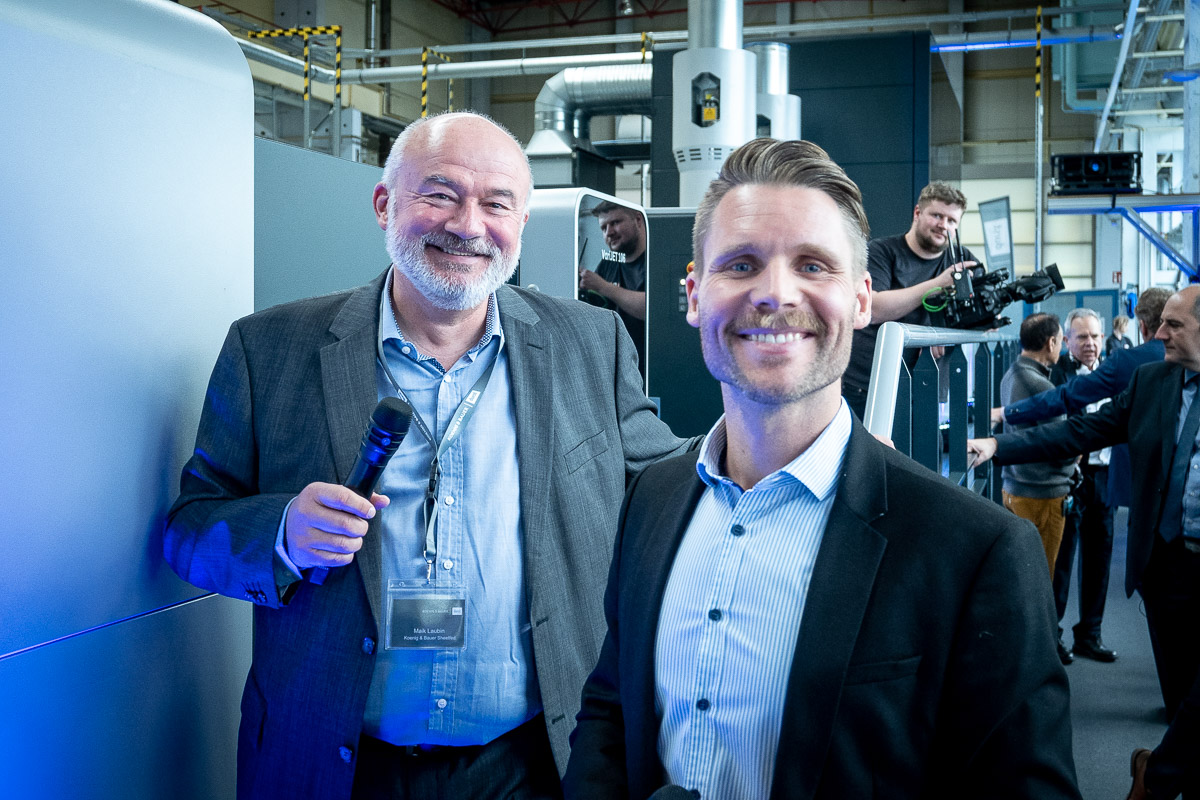
Maik Laubin (left), Global Sales, VariJET 106, and Pierre Hertzell, VariJET 106 Product Manager presented at the event
At the same time average runs are falling with operations under pressure to manage many more short-medium runs. Sean pointed out that a shift in all carton volume from 26% to 29% equates to 20 million more jobs and asked: “How do you manage more jobs in your shop effectively?”
Robert Stabler detailed how to build a business case in digital printing in folding carton markets and outlined key solutions developed for carton converters.
He highlighted how the latest technology in the modular VariJET 106, that can utilise offset and flexo functionality, helps future proof investment. The B1 5,500sph press platform for folding carton packaging makes simple work of limited-run seasonal and personalised, targeted packaging.
A water based, food safe and deinkable ink set, developed with exceptional rub resistant characteristics, ensures food safe production meeting current and future regulatory and environmental standards. The most recent of which is the updated The Packaging and Packaging Waste Directive that aims to ensure that all packaging is reusable or recyclable in an economically feasible way by 2030.
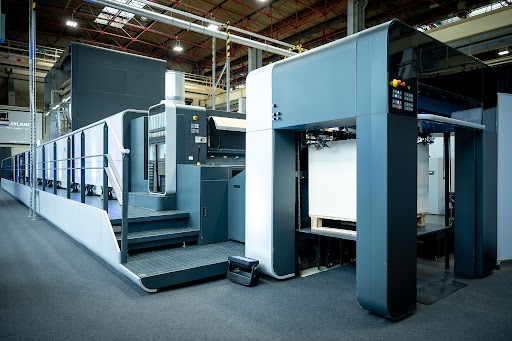
VariJET 106: Leveraging the know-how and expertise of Durst and Koenig & Bauer, two giants in the printing and packaging industry
The VariJET 106 leverages the know-how and expertise of Koenig & Bauer’s leadership in offset printing with Durst’s digital inkjet prowess. This enables the delivery of offset quality while harnessing the flexibility of digital allowing customers to build new, highly responsive business models. Based on Koenig & Bauer’s standard high performance Rapida 106, it features standard components for infeed, priming, coating and delivery. It incorporates Durst printhead electronics, inkjet expertise, proprietary workflow, and RIP technology.
Highly automated file submission, approval and delivery to the press is managed by Durst Workflow. It also automates unique coding and numbering applications for track and trace applications. The optional Smart Shop module provides a full e-commerce front end, including design and job submission tools while the comprehensive analytics tool set, reports detailed performance data and KPIs that aid press optimisation.
All of which help contribute to a convincing TCO (total cost of ownership) when evaluating whether an investment will pay off, where the volume break even points are to ensure more accurate costings, and how the most effective technology utilisation can be achieved. Other benefits such as how digital just-in-time print production can help reduce storage costs and obsolescence were also explored.
Attendees watched as the press was put through its paces and seamlessly ran five carton jobs in just over 15 minutes, which included job-changes on the fly at a top speed of 5,500sph. “Don’t blink or you’ll miss it!” Three featured the same stock with design and ink coverage changes. Next was a spot varnished job on a different board with a changeover of varnish plate. The final job included board size change and another spot varnish.
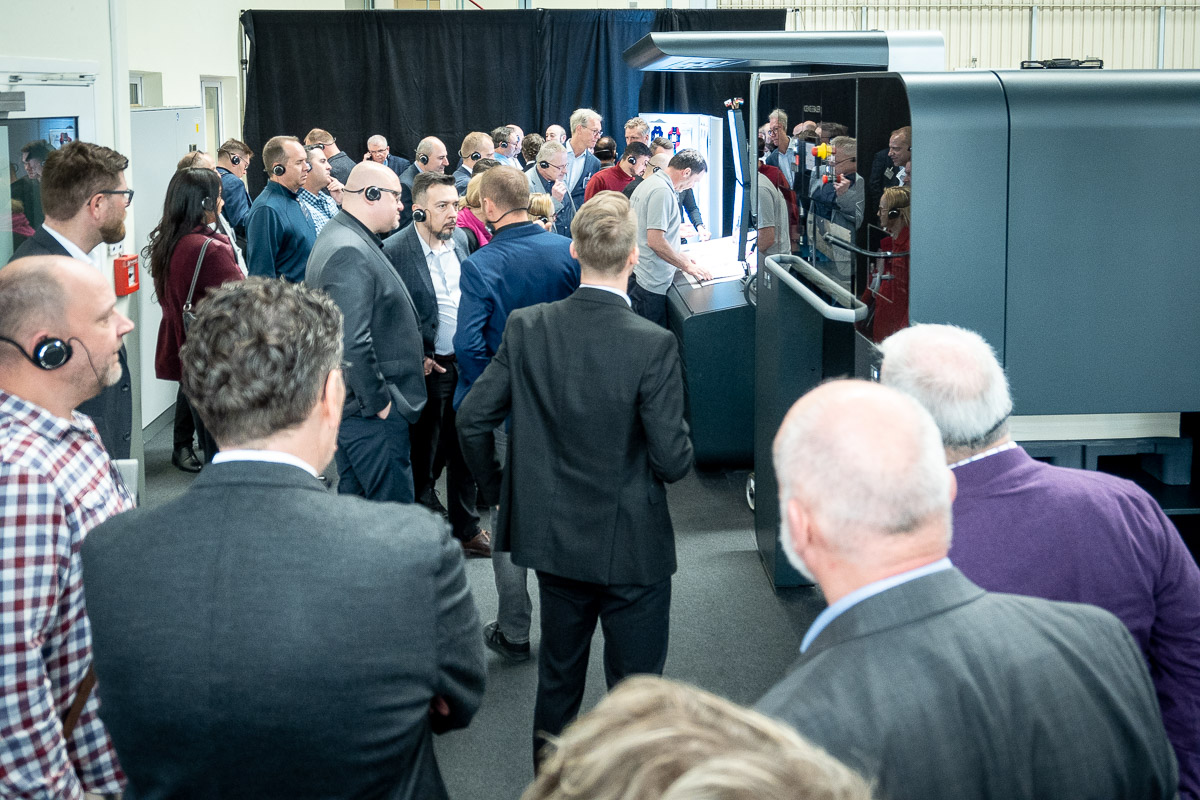
Delegates witnessed job-changes on the fly at top speeds of up to 5,500sph on the VariJET 106
The event included updates on the installation of the first beta press that will be up and running this month (May). Preparations are underway to install a second in June and a commercial customer is planning production from Q3. Other systems are under construction.